Kubus
Makes Processing Even More Efficient. Van der Plas is in constant evolution, evident on our website showcasing our new corporate identity. Beyond aesthetics, we are dedicated to innovation, ensuring every florist receives the finest flowers and plants at a fair price. This commitment to innovation led to the expansion of the Kubus, our revolutionary order distribution system for customers of wholesale businesses. In this blog, you'll discover everything about the upgraded Kubus!
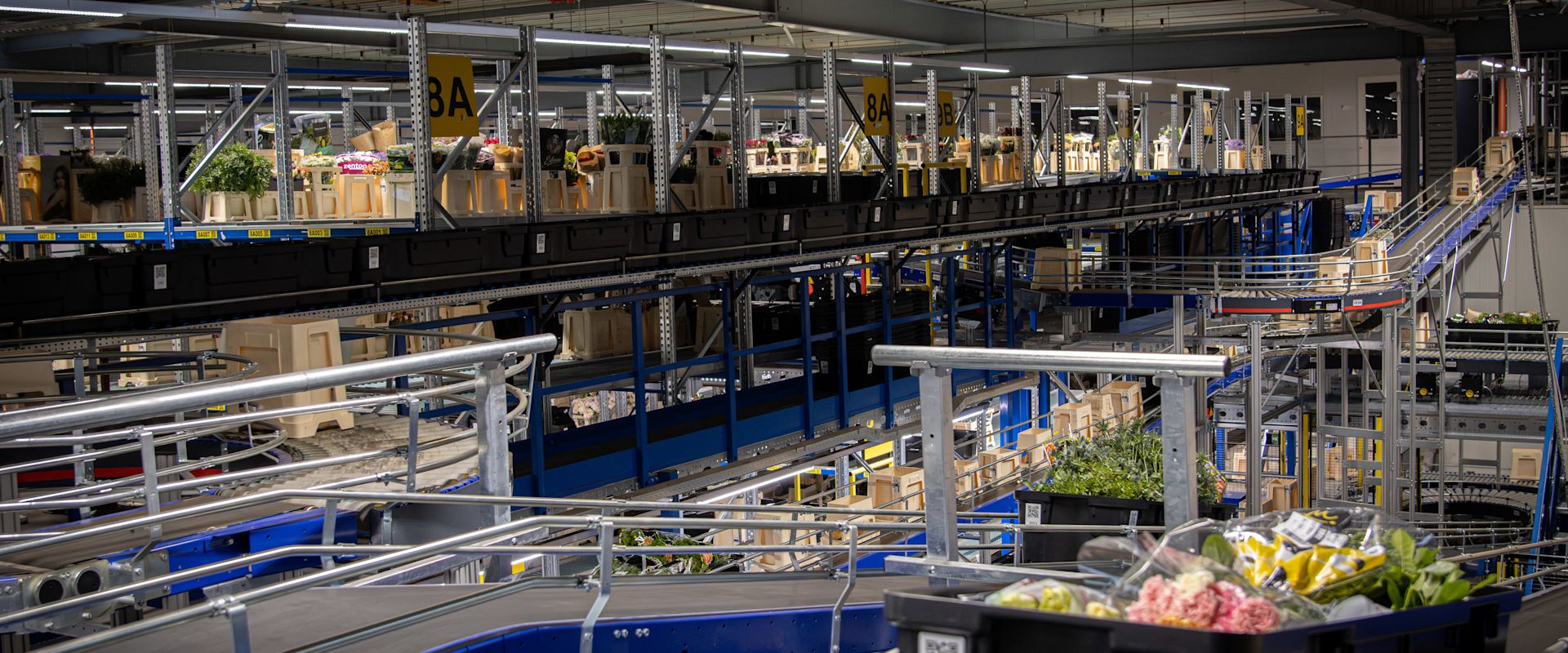
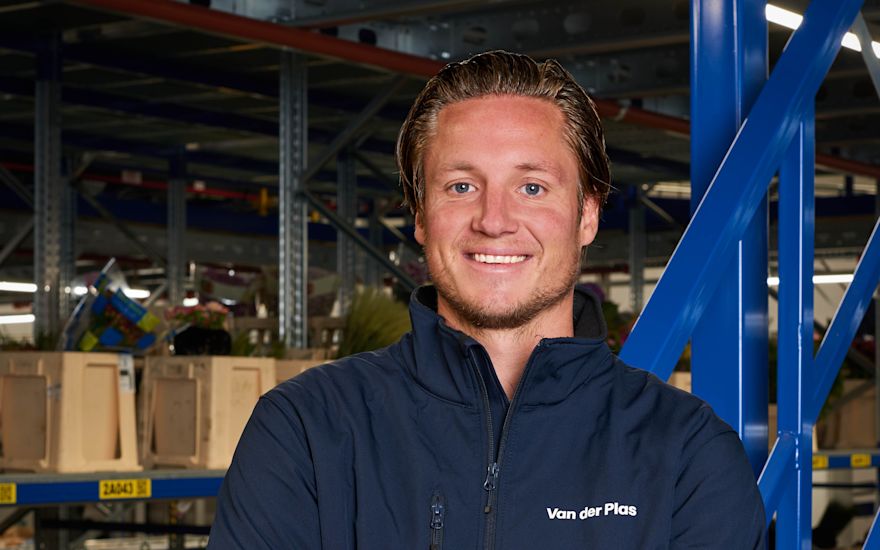
What is the Kubus?
The Kubus is a steel structure with a total of 12 kilometers of conveyor belts, where order picking and distribution take place. There are a total of 15 Kubuses ensuring the swift processing of all orders. Sander van der Gugten, the brain behind the Kubus and a process engineer at Van der Plas, explains, "Thanks to the Kubus, we can offer an extensive range of flowers and plants while ensuring speedy and comprehensive processing. We distribute cut flowers at the customer level, making orders ready sooner, and flowers depart for florists more rapidly. Additionally, the Kubus significantly reduces the margin of error."
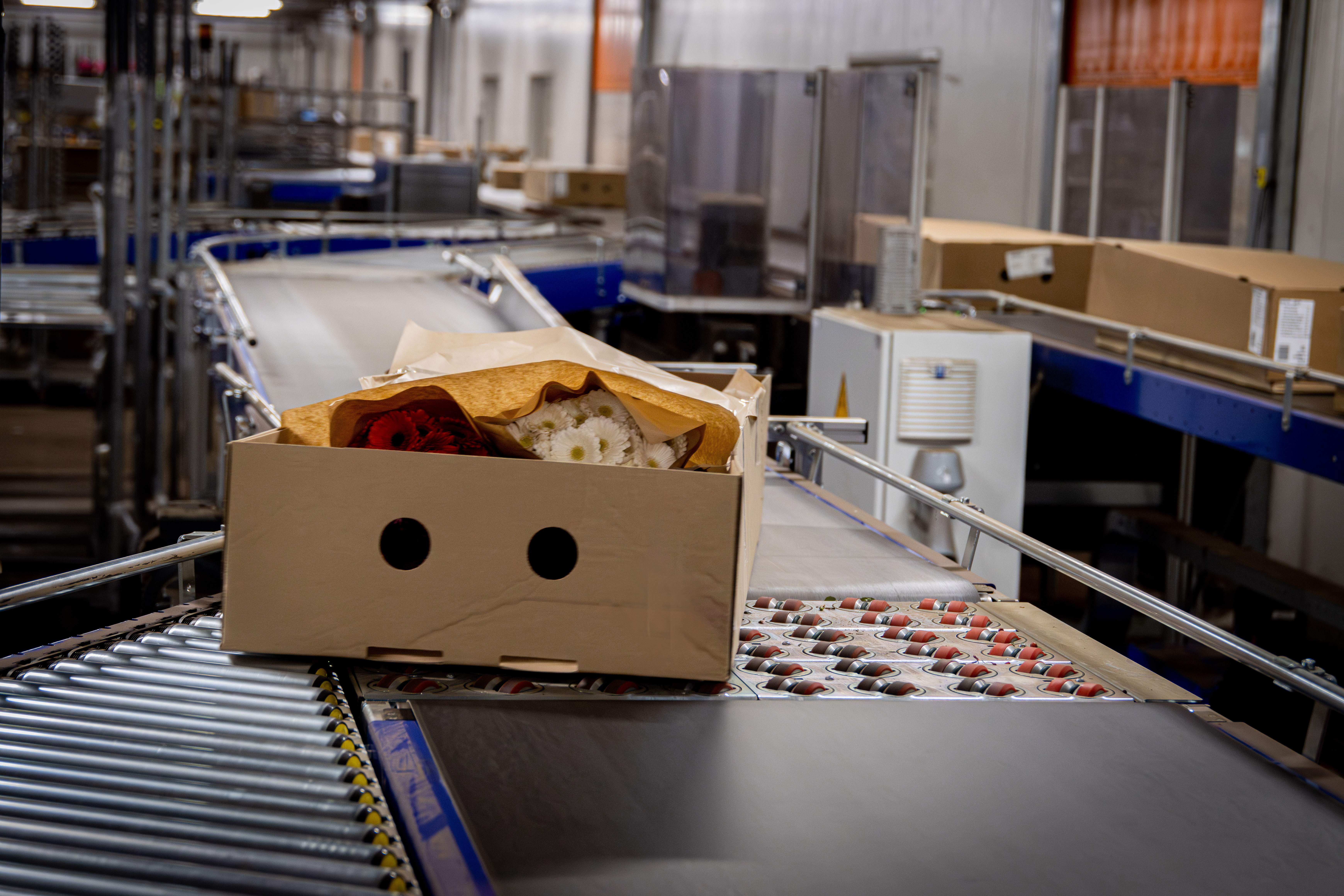
Expansion
Recent expansions to the Kubus streamline the order processing even further. In 2022, the Pitstop was added, ensuring a more constant flow in the process. In October this year, the Finish was introduced, an extension of the number of exits on the packing belt. With ten exits instead of seven, it is now possible to process even more customer orders at an accelerated pace. The introduction of the Strip in December connects the Kubus directly to the packing process, eliminating crates and carts from the process. This further increases the speed of the processing system.
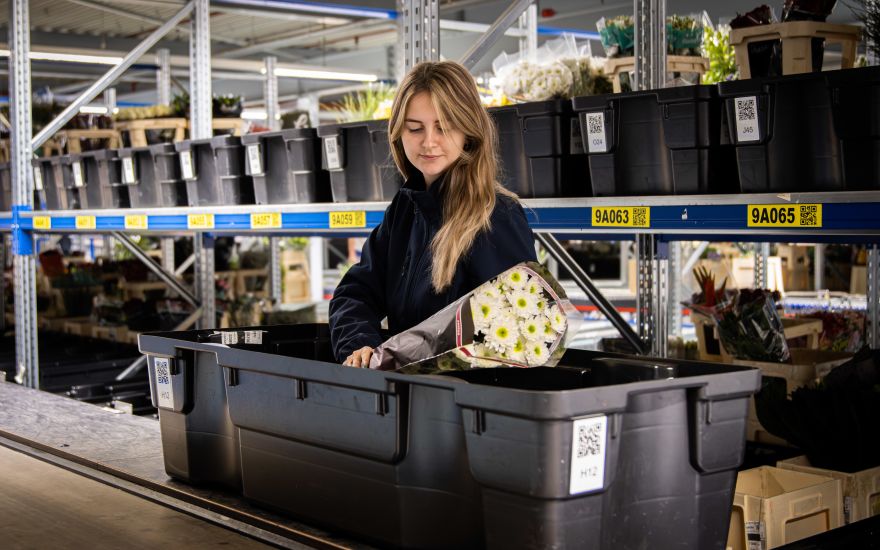
Results
The expansion of the Kubus enables Van der Plas to meet the rapidly growing demand. The results speak for themselves. Since the introduction of the Kubus, the productivity of flower order picking and distribution has increased by 13.5%. Additionally, the number of credit invoices due to incorrect or damaged orders has decreased by 13.1%. Furthermore, the number of flowers written off due to processing errors has dropped by 94.9%. With the introduction of the Strip, these results are expected to further improve.
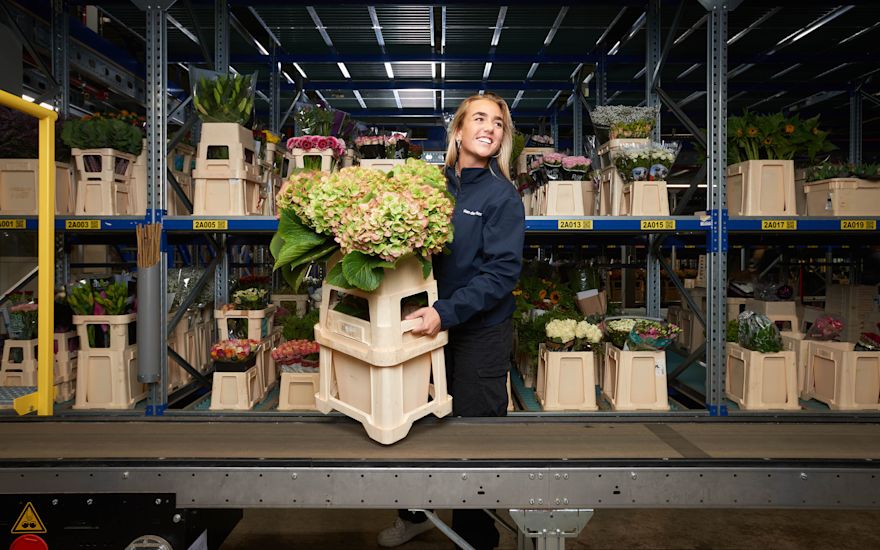
Efficiency and Job Satisfaction
Someone witnessing the impact of the Kubus up close is Hans Barnhoorn, who leads the employees working in the Kubus at Van der Plas. "It's a great way of working," says Hans. "I always find it a fun challenge to make order processing run as smoothly as possible. The revamped Kubus certainly aids in this. The work is more efficient, and clearer, and the regular staff also enjoys working with this system. Job satisfaction and motivation contribute to a smooth process, which is important to me.”
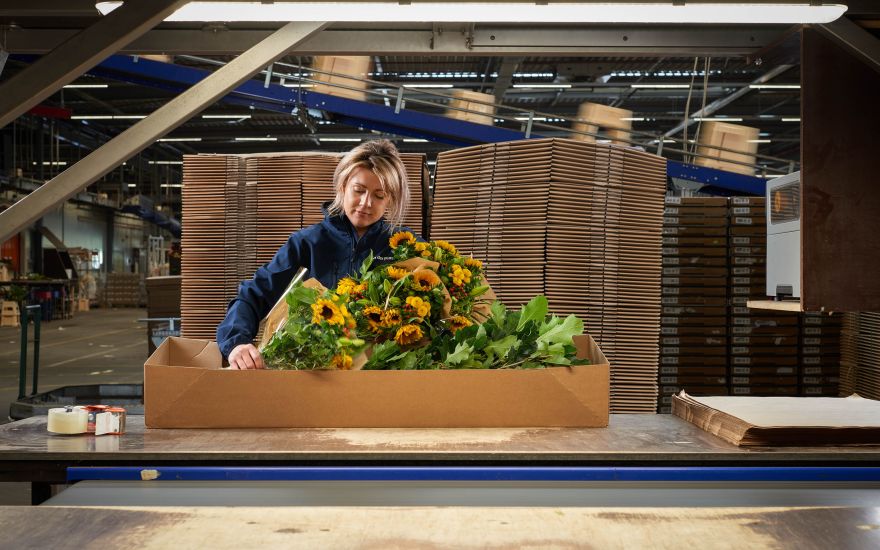
Reduced Physical Strain
Lisanne de Winter, who has a managing role in the packing department at Van der Plas, is also positive about the expansion of the Cube. "With the addition of the Strip, we are already doing the packing on the Cube without having to work with kegs and carts. After scanning the QR code, you immediately see what should be in the crate and what packing material to use. This makes the process much faster and fewer mistakes are made. In addition, the work is much less strenuous because you don't have to put casks on the belt or lift heavy flowers off a cart."
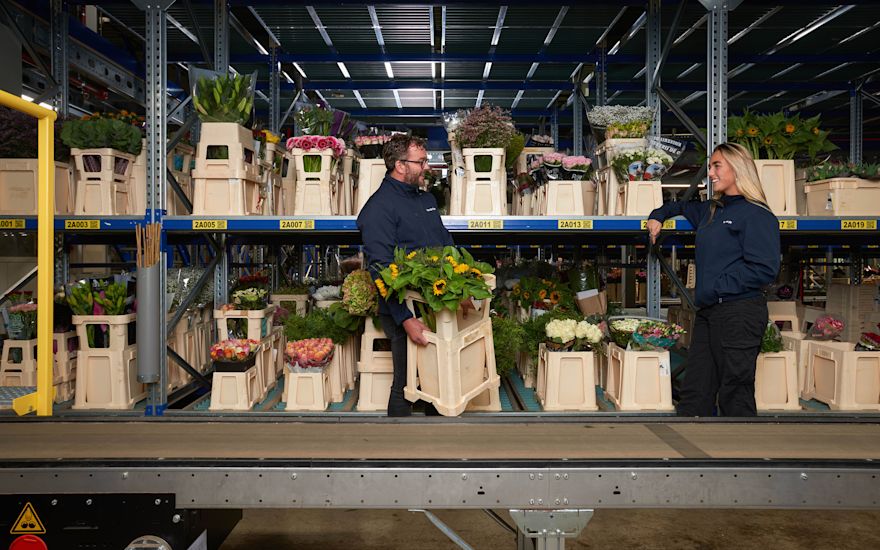
Working with Kubus
Lisanne says the colleagues in the packing department are very positive about the additions to the Cube. "From day one, everyone thought it was super. Also for me, it's very fun and interesting to see how this extension of the concept has been brought to fruition."
After reading this blog, are you as excited about working with the Cube as Hans and Lisanne and would you like to work at a cozy family business? Then check out the vacancies at Van der Plas immediately! Who knows, maybe we will see you soon at our office for a good conversation!